Roller Crusher Discharge Size How To Adjust The Adjustable?The gap adjustment of roll crusher is the core operation to control the granularity of the discharged material, which is mainly realised through the mechanical adjustment device, wear compensation and operation optimisation. The following are the specific adjustment methods and precautions:
1、Mechanical adjustment device
Wedge-shaped adjustment device (mainstream)
Principle: Control the position of the wedge by rotating the adjusting bolt. When the bolt is pulled upward, the wedge opens the movable roller, the gap between the two rollers increases, and the material is coarser; when the bolt is pushed downward, the spring presses the movable roller, the gap decreases, and the material is finer.
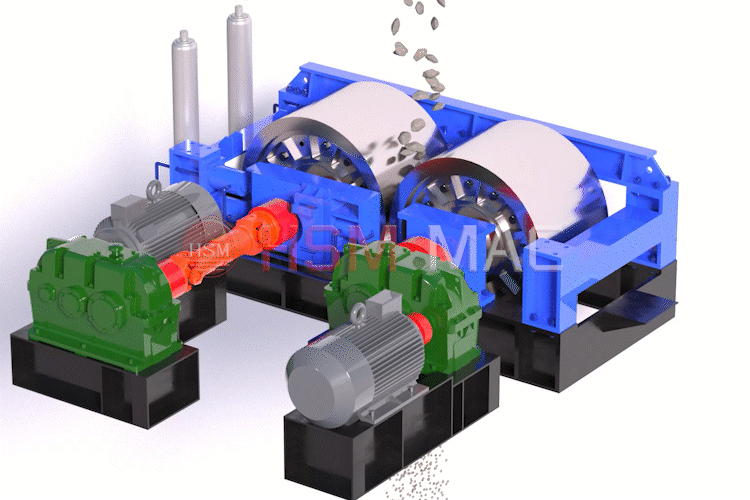
roller crusher Working Principle
Operation steps (take the laboratory model as an example):
Firstly, tighten the adjusting handwheel clockwise to the state of no gap between the two rollers;
loosen the handwheel counterclockwise, and the gap increases by about 3mm for each revolution;
lock the nut after adjusting to the target gap to ensure that the two rollers are parallel.
Gasket adjustment device
Principle: increase or decrease the number or thickness of shims between the frame and the movable bearing. Increase the gap when increasing the shims (the output material becomes thicker), reduce the gap when decreasing the shims (the output material becomes thinner).
Characteristics: It needs to stop the machine for operation, and is suitable for the basic model without automatic adjustment function.
2、Auxiliary adjustment methods
Roller speed control
Increasing the speed can increase the number of crushing times, and the discharged material will be finer;
decreasing the speed will make the discharged material coarser. The roll gap needs to be adjusted to suit the hardness of the material .
Uniform feeding optimisation
Uneven feeding will lead to uneven wear of the roll surface and formation of grooves affecting the size of the discharged material. Use a feeder that matches the length of the roll to ensure even distribution of material along the entire length of the roll.
3、Wear compensation and maintenance strategy
Roller skin wear compensation
After the roller skin is worn, the gap increases, and the discharged material becomes coarse. It is necessary to check regularly (recommended once every 3 months) and readjust the gap.
Lubrication and cleaning
Bearing every 3 months with calcium-based grease grease, chain weekly refuelling and monthly diesel cleaning.
Stop the machine to clean the sticky material blockage to avoid affecting the gap precision.
4、Safety operation specification
Preparation before adjustment
Adjustments must be made without stopping the machine
Installation of iron removal device to prevent metal debris damage to the roller.
Material adaptability control
The feed size needs to be ≤ 80mm (hydraulic model), when the hardness is too high with the jaw pre-treatment.
Sticky materials are easy to clog, need to stop the car to deal with.
5、Verification process after adjustment
No-load test run: idle for ≥2 hours after adjustment, check the temperature rise of bearing (≤30℃), noise and vibration.
>Load test run: feed running ≥ 8 hours, monitor whether the particle size of the discharged material meets the requirements, bearing temperature rise ≤ 35 ℃.
>Particle size test: if the discharged material does not meet the standard, it is necessary to re-adjust the gap or check the wear of roller surface.