Is the roll crusher resistant to wear and tear?Wear and tear of roll crusher mainly comes from three aspects: nature of material, equipment factors and operation mode. The hardness, humidity and particle size of the material are the main factors affecting wear. For example, materials with higher hardness have a more significant effect on the wear of the equipment. Equipment factors include roll material, structure and design. If the roll material is not properly selected or the structure is not reasonably designed, the wear process will be accelerated. Operation methods such as feeding speed and load size will also affect the wear situation.
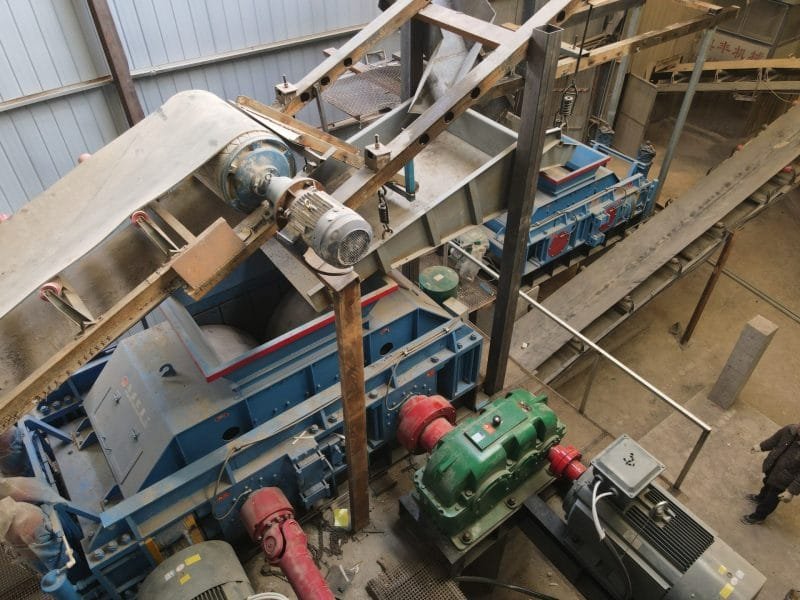
Roll crusher
Wear prevention measures for roll crushers:
The rollers are made of high chromium alloy, high manganese steel or special alloy materials to improve the anti-wear performance. For high hardness materials such as river pebbles, increase the thickness of the roll surface or use wear-resistant coating technology (such as spraying tungsten carbide). Improvement of structural design.
Reduce the friction by optimising the shape of the roll surface (such as spiral teeth, grooved teeth). Adjusting the roller gap to a reasonable range (usually 0.1-5mm), and adopting the differential speed design to make the two rolls rotate at different speeds. So as to reduce the risk of local abrasion.
Reasonable regulation of operating parameters
According to the hardness of the material, dynamically adjust the feed volume, roller pressure and speed to avoid overload or idling. For example, high hardness materials need to reduce the feed speed and increase the roller spacing. Uniform distribution and particle size control.
Ensure that the material is continuously and evenly distributed on the roll surface to prevent partial grinding. Pre-screening to remove oversized particles (such as materials exceeding 1/20 of the roll diameter) to reduce impact wear.
Regular Inspection and Replacement
Daily inspection of bolt tightness, bearing sealing and lubrication status. Test the depth of wear on the roll surface every 3-6 months. If the groove is more than 5mm it needs to be repaired and ground or replaced. Establish a preventive maintenance programme, including overhaul every 1200 hours and overhaul every 2400 hours.
After stopping the machine, clean up the accumulated material in the roll seam in time to prevent impurities from aggravating the wear. Lithium grease lubricates the bearings regularly. Increasing the frequency of lubrication in high temperature environments. And configuring the cooling system to control the temperature of the rollers.
Wear and tear on a roll crusher is the result of a number of co-ordinated aspects of materials, design, operation, maintenance and technological upgrades. The roll crusher of Huashengming Heavy Industry uses high chrome alloy rolls + intelligent monitoring system. Which extends the roll life to 1 year and reduces the maintenance cost by 40%. Flexible adjustment of the programme in combination with the characteristics of materials (such as hardness, humidity) during implementation.